How HOLMER reduces downtimes with synthavo
Service in the agricultural sector is struggling with high demands in terms of machine availability combined with high wear and tear on parts. Machine manufacturers who ensure high availability and fast repairs will dominate the market.
With synthavo, HOLMER differentiates itself through outstanding service that not only saves nerves but also downtime.
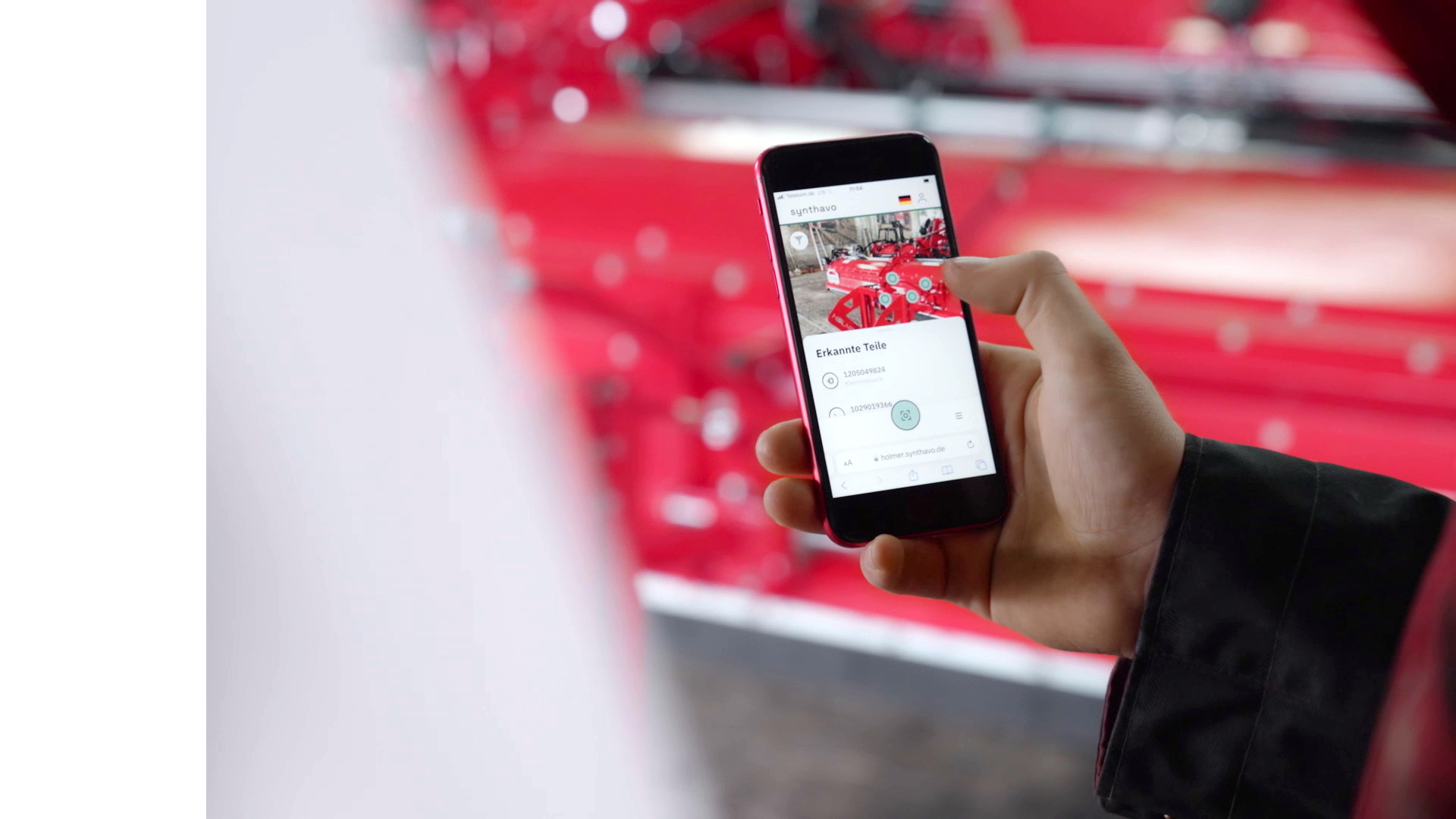
High wear and tear, quick repairs
The machines are constantly exposed to harsh conditions during use. To guarantee a successful harvest, repairs must be carried out efficiently, quickly and effectively.
HOLMER is the technology leader in beet lifting technology. The high level of wear and tear in agricultural technology makes identifying spare parts an everyday task. The parts are often in a heavily soiled and worn condition.
Until now, spare parts have been identified using a physical or digital spare parts catalog.
The process is time-consuming and prone to errors. Parts are ordered incorrectly and HOLMER has high support costs.
Reduce service costs, make repairs more efficient
With synthavo's 1-Click Spare Part Identification, the spare part is identified with just one photo. The recognition also works in a heavily soiled or worn condition - perfect for agriculture. Recognition via smartphone as a supplement to the spare parts catalog reduces incorrect orders.
Repairs are more successful and efficient. Harvesters are back in use more quickly. HOLMER has lower support costs.
At synthavo, the machines are on-boarded to the solution fully automatically. We are familiar with the wide variety of machines used in mechanical engineering and therefore design our solution with minimal effort for our customers. From mechanical engineering, for mechanical engineering.
"The cooperation with synthavo is totally uncomplicated for the manufacturer.[...] Very little implementation effort is required on our side. All the work is done by synthavo, which naturally takes a lot of pressure off us as the manufacturer."
- Julian Leinbach, Head of Customer Service, Holmer Maschinenbau GmbH
.gif)
By implementing synthavo's 1-Click Spare Part Identification, HOLMER not only optimizes efficiency in the identification of spare parts, but can also realize significant economic benefits:
The precise and error-free identification enables HOLMER customers to identify their spare parts quickly and unambiguously. The 1-Click Spare Part Identification is an effective measure to reduce incorrect orders for the manufacturer and the customer. Unnecessary service calls are avoided, spare parts are ordered faster and more efficiently, downtimes are reduced and the overall uptime of the machines is increased.
"Thanks to the successful use of synthavo, HOLMER is retaining its customers in the long term and can therefore increase sales and profitability in the spare parts business," says Sebastian Stöcklmeier, CEO of synthavo.
The 1-Click Spare Parts Identification and the convenient and effective service experience differentiate HOLMER in the market and position the company as a pioneer in the industry.
The better the service, the better the customer loyalty. The advantages for the customer are accuracy and speed, just like with our own technicians. This saves us a lot of downtime.
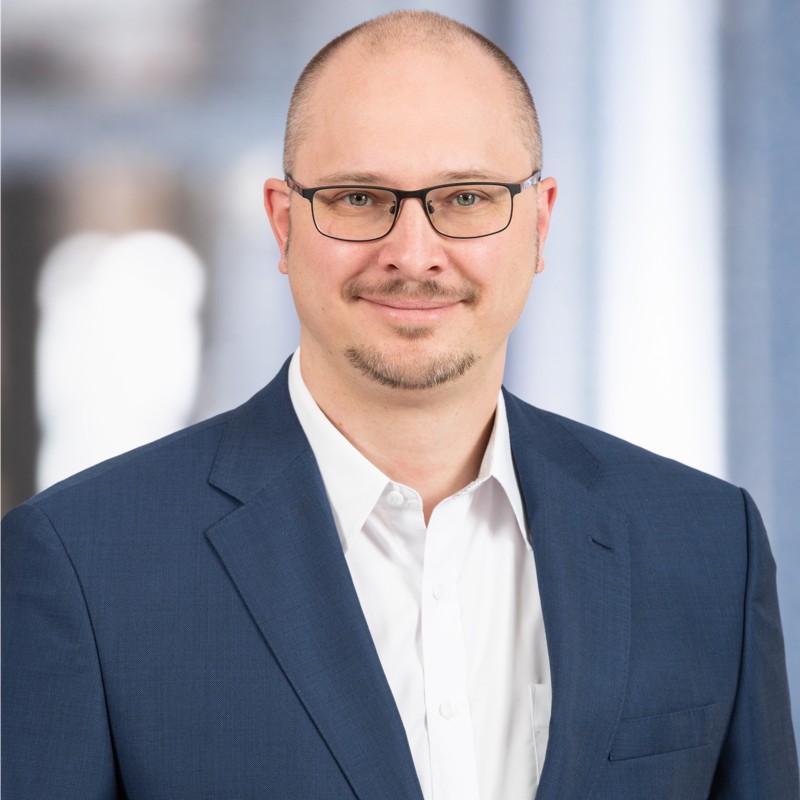
.png)
Boosting new machine business
The success of machine sales is increasingly dependent on excellent service. Thanks to the 1-Click Spare Part Identification, HOLMER's service differentiates itself from the competition and thus sustainably drives the new machine business.

Customer Lock-In
The 1-Click Spare Part Identification is directly linked to HOLMER's sales channels. This means that customers are routed directly to HOLMER's sales channels. The result is stronger customer loyalty and increased spare parts sales.

Service-Efficiency
The previous spare parts identification process resulted in high costs for HOLMER due to incorrect orders and support services. Now, with the help of the 1-Click Spare Part Identification, these costs are massively reduced and the efficiency of the process is increased.
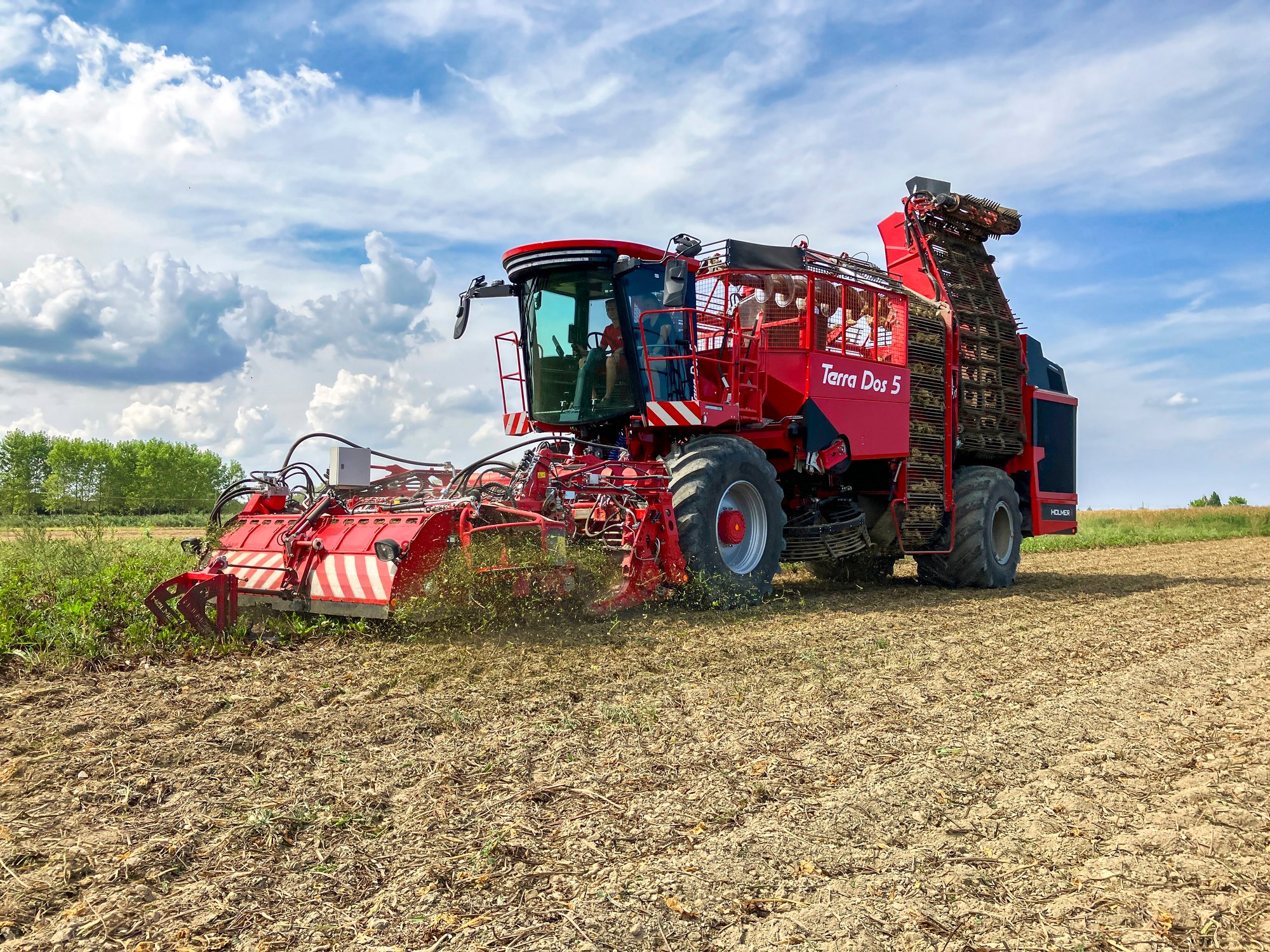
HOLMER
With over 50 years of experience in agricultural technology, Holmer stands for innovative solutions to meet the increasing demands of modern agriculture. HOLMER specializes in particular in the production of high-performance beet harvesters and self-propelled harvesters, which are internationally recognized for their efficiency and advanced technology.